Quick Links
Related Topics
It's probably happened to you before. You buy something online and are so excited when it finally comes in. Instead of the item you were expecting, you received something different or your item came broken or incomplete.
Your disappointment is what your customers feel if your business ships out bad products. A pre-shipment inspection (PSI) aims to prevent this problem.
If you want to minimize faults and ensure your products are thoroughly prepared for shipping, we can help. Keep reading to learn about a pre-shipment inspection procedure and what it means for your business.
What is a Pre-Shipment Inspection?
A pre-shipment inspection procedure refers to the phase in freight shipping where you can address problems before receiving and paying for goods.
An inspection company will assess the goods before shipping them out. Your business can defer your final payment of the products until you receive a pre-shipment inspection report.
This process can only occur when all ordered units have been manufactured and 80% have been packed. These rules are in place to avoid examining the best samples.
Pre-shipment quality control is beneficial for businesses. Some believe that this procedure can cause delays, but a great inspection company will work to ensure this doesn't happen
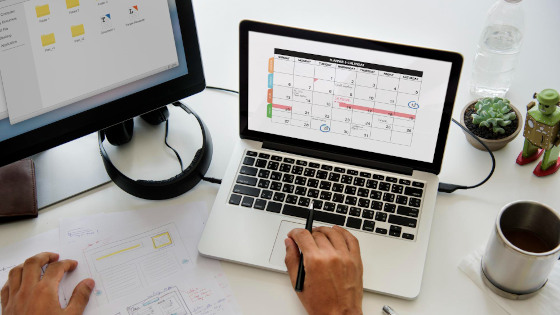
What are the benefits of a Pre-Shipment Inspection?
Dealing with customer complaints, customer returns, and gaining bad reviews can cost your business a lot of money.
Pre-shipment inspection is a highly effective and efficient method to identify and correct product defects before shipping. It helps to detect product defects while they are still at the factory site and before they are sent to your customers. This allows the supplier to perform any necessary re-working to avoid supplying non-conforming products to your destination market. Additionally, pre-shipment inspection helps to ensure that your production remains on schedule, enabling you to meet your shipping deadlines.
Identifying imperfections that could affect the functionality or appearance of the product can help in two ways. First, your business can maintain product quality. Second, you mitigate your risk of complaints and returns from buyers.
Importantly, a pre-shipment inspection helps to ensure your products meet regulatory and compliance requirements.
Some of the most important reasons to have a pre-shipment inspection include:
- Ensuring samples accurately represent mass production
- Verifying product quality and quantity
- Ensuring goods are up to your standards
- Safeguarding your brand reputation
- Assuring your products are functional
In addition to checking product quality, an inspection company will check product paperwork for errors.
Inspectors will review shipping certifications, documents, and other relevant papers. This helps ensure shipping standards are compliant with import and export regulations.
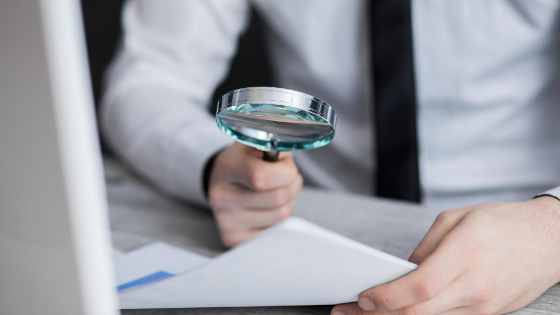
Pre-Shipment Inspection Procedure: The Steps
There are specific steps involved in a pre-shipment procedure. The amount of time an item is in the pre-shipment inspection process typically depends on the sample size.
Order Placement
Choose the date you want your inspection to occur. As a general guideline, it's recommended you book your inspection at least a few weeks in advance to ensure you can secure an appointment that fits your timeline.
Next, you want to let them know where your products are in their production status. Ideally, you want your products to be at least 80% completed for a pre-shipment inspection. This benchmark ensures that the inspection covers the majority of the product's manufacturing process.
An inspector will use an inspection checklist of quality control criteria. The checklist will help maintain accuracy and consistency throughout the inspection process.
Make sure you communicate your product requirements to the inspection agency. With eAQF, you can upload a document if there are any specifications or requirements.
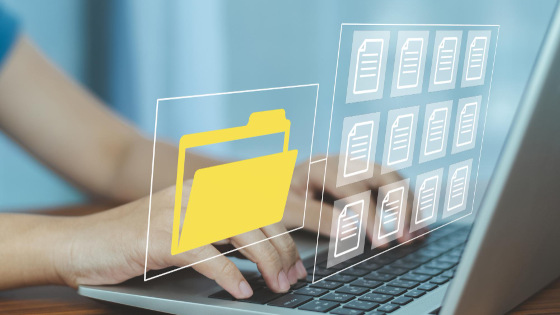
Inspector On-Site Will Be Your Eyes and Ears
Once your inspection order is received, our team will communicate with your supplier to confirm the inspection location and the feasibility of your required date. In most of the cases, your order will be conducted on your requested date. If the supplier is unavailable on your requested date, we will confirm with them a feasible date and inform you for visibility.
The inspector will run a non-discriminatory, transparent procedure while protecting sensitive business information, which helps to products comply with trade secrets and intellectual property rights. This is important if you deal with patented technology or proprietary designs.
During the inspection, the inspector will document all the issues found in a detailed report. This report includes photographic evidence of the defects, descriptions of the problems, their location, and severity, and the defects will be classified as minor, major, and critical.
Keep reading below for an in-depth description of what happens during a pre-shipment inspection.
Quantity Check
An inspector will count the shipping cartons to confirm how many items are in shipping condition. The quantity needs to match the purchase order correctly.
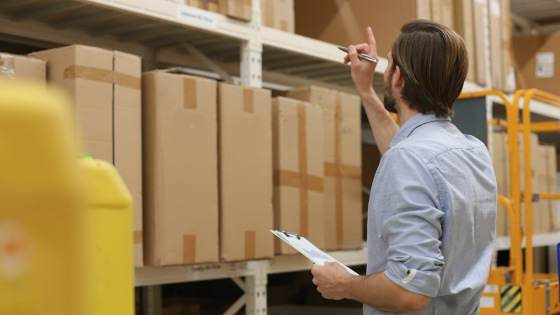
Random Sampling
The inspector will complete a random evaluation by choosing any product sample. Random sampling allows the quality control team to estimate the quality levels of the entire batch of manufactured goods.
Accredited pre-shipment inspection services use the same internationally known Acceptable Quality Limit (AQL). The number of items selected is the maximum number of defects allowed in one batch before it gets rejected.
Workmanship Check
An inspector will look at the overall appearance of the random products for visible flaws or production defects. Inspectors will check for discoloration, dents, scratches, and other imperfections.
Flaws are assigned to minor, major, or critical categories based on tolerance levels.
The Acceptable Quality Limit (AQL) defines the tolerance levels. If the defect number is within the limit of AQL, the result will show “Pass”, otherwise the result will be “Fail”.
Volume and Functionality Verification
The inspector must check the size and dimension of products to ensure that the height, length, width, and weight comply with your specifications.
A functionality verification will test that the items are working as they are designed to. This step of the process is generally dedicated to footwear and garments.
On-Site Test
On-site test is one of the most important steps in the inspection process. No matter what your product is, a pair of sneakers, a microwave, or a plush toy, on-site tests apply to check the real-life functionality of your product.
For example, if you sell furniture, on-site tests will check aspects like hand feeling, smell, stability, and sharp edges to ensure this product is functional for daily use.
If you sell a home appliance like an ice maker, on-site tests will check if the machine can open or shut down properly, if it gets overheated when used, or if it can make enough ice cubes.
Wherever you are selling, Brands and Online Sellers must ensure legal requirements of the destination market are met. To help avoid regulatory problems, inspection services will check that certificates and reports are in order.
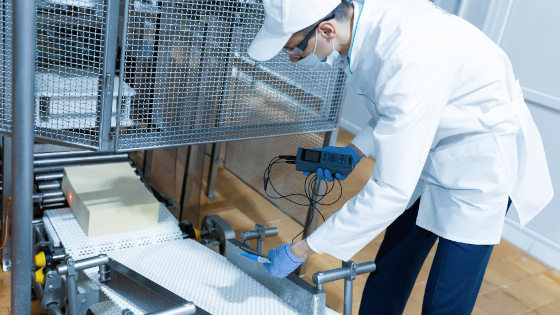
Inspection Report
Lastly, all of the information gathered from each step is combined into a thorough inspection report. An inspection report typically contains detailed information about the findings, observations, and evaluations made during the inspection process.
The main points in an inspection report include the following:
- General information about your products
- Summary and overview of each check
- Inspection findings on non-conformity
- Photographic evidence on defects found
- Photographic evidence on on-site test results
- Final inspection result that indicates pass, fail, or pending
An inspection report from a trusted third party can show buyers that your products meet quality requirements. The manufacturer and supplier will also receive valuable feedback on their goods. The detailed report will highlight areas for improvement so that manufacturers can make adjustments to enhance product quality.
This fosters better communication between the buyer and the supplier, building stronger and longer-lasting business relationships.
When Should I Schedule a Pre-Shipment Inspection
During the production process, different inspection types shall be applied at different manufacturing stages. A pre-shipment inspection is usually conducted when 80%-100% of your production is finished. Here are some key considerations when defining when to schedule a pre-shipment inspection:
- What is my production timeline? Schedule the pre-shipment inspection when 80%-100% of production is complete, aligning with the critical stages of your production timeline.
- When is my shipping deadline? Coordinate the inspection to meet shipping deadlines, leaving a buffer for any corrections so deadlines are met.
- Is there a seasonal peak? Consider peak demand periods to align the inspection with heightened production, meeting customer expectations during seasonal peaks.
- Is my brand making a new product or using new material? Arrange inspections when the risk level is higher than usual, for example, when you are producing a new product with new specifications, or using a new material with uncertainty.
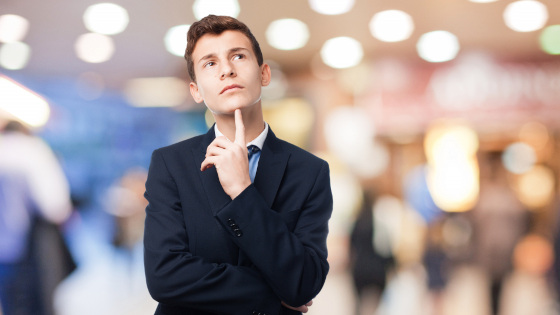
Also, you may consider conducting pre-production inspection (PPI) before your mass production runs, and during-production inspection (DUPRO) when 10%-60% of your products are finished to identify risks early and ensure your product quality all along your production line.
Considerations When Selecting a Pre-Shipping Inspection Company
Firstly, companies with experience in your specific industry or product category is invaluable. At eAQF, we have qualified and experienced inspectors across the consumer product industry, including textile, furniture, cookware, home appliance and more. This will make sure your quality control partner can understand your requirements, offer adequate support, and assist when expanding to other categories.
Check the company has the necessary certifications and accreditations relevant to your industry or the type of inspection needed.
Check if the company offers the type of inspections you require. Some might specialize in certain types of goods or inspections, while others offer a broader range of services.
Secondly, compare turnaround times. In this fast-changing market, turnaround times can contribute to quicker decisions and help to fit your shipping and marketing schedule.
Thirdly, look for companies with a global presence. In many cases, online sellers source from overseas suppliers, and your inspection company needs to be located near the regions where your products are being manufactured or shipped from. A company like eAQF is a good fit as we have teams in all major manufacturing locations.
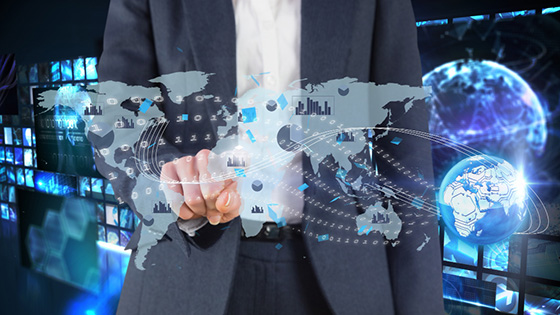
Assess if the company can accommodate any unique requirements you may have. Some companies offer customizable inspection services to suit specific needs. A company that is attentive, responsive, and willing to tailor their services according to your unique requirements can significantly enhance the inspection process.
Your Products Are Our Priority
At eAQF, your products are our priority. We help to ensure your products meet your customers' expectations, save you time and money, and enhance your brand reputation through our professional pre-shipment inspection services.
Working with eAQF can make your life easier. With eAQF, you can book and manage quality control solutions easily online, receive and review your quality reports immediately once they are ready, and access real-time data 24/7. Are you ready to improve your e-commerce business with effective quality control? Register for eAQF today and get started!