Quick Links
Related Topics
Quality Control is a procedure used by brands and retailers to ensure their products meet their required quality standards. Among all the quality control solutions, product inspection is one of the most-used solutions.
These inspections follow a set checklist of requirements that apply to every aspect of a product. This includes checking the materials, appearance, functionality, and safety of manufactured goods.
There are several types of inspection protocols for each stage of the production process. Keep reading to discover why inspections are important and explore various quality control inspection examples.
What is the role of Inspections in Quality Control?
Most Brands and Retailers rely on third parties for various aspects of their production process. They must outsource the materials, manufacturing, or packaging of their products.
Online sellers rely entirely on outside sources when procuring their products. In many cases, these sources are located many miles away, if not in another country entirely.
In these cases, it's important to outsource quality control services to a reliable third party who can act on your behalf in these locations.
Businesses need to maintain strict quality control during production to avoid costly mistakes. Even a small error can lead to negative consequences such as expensive recalls, poor customer ratings, and significant sales declines. By scheduling regular quality control inspections, businesses can take a proactive approach to ensure their products meet the set quality specifications and prevent these expensive issues.
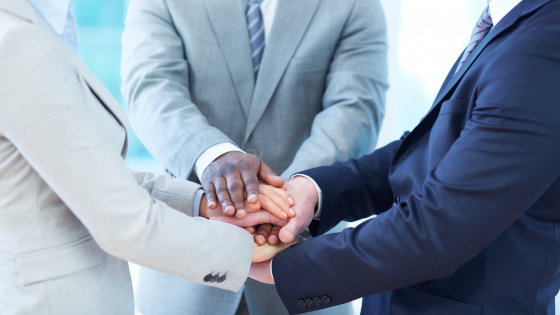
These quality control measures have significant benefits for both online and offline sellers, namely:
Convenience and Peace of Mind
Hiring a reputable third-party inspection service is imperative for business owners who can't inspect the products they're selling in person. It's one of the most effective ways to ensure you're getting the quality you expect from the items you order.
In many cases, hiring a neutral third party can have additional benefits, too. These include:
- An unbiased opinion
- Training and expertise
- Cost savings from the early detection of issues
Customer Satisfaction
High-quality items reflect well on your business and lead to repeat sales. Poor-quality goods will damage your business reputation and can result in complaints, negative reviews, lost sales, and even lawsuits.
Increased Efficiency
Performing quality inspections at various stages of the production process helps identify inefficiencies and streamline manufacturing processes. When you center your quality inspections on the end product only, you miss these opportunities for improvement.
Ensuring Compliance
Every destination market has certain standards that ensure the safety and satisfaction of the consumer. For instance, in the USA, all products aimed at children must undergo lab testing to guarantee the safety of young users.
Amazon also has strict quality control measures in place for sellers who want to take advantage of their streamlined order fulfilment systems. If you're one of the millions of third-party sellers who are active on this platform, you must engage with an FBA specialist inspection company to ensure you meet Amazon’s strict requirements.
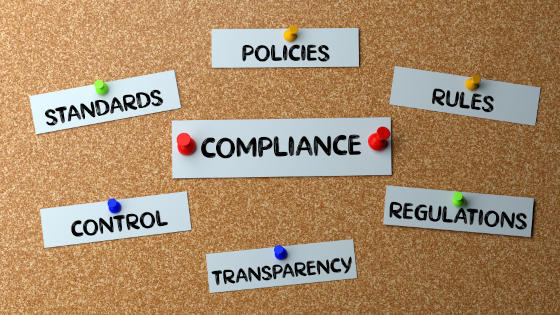
Reduce Cost
Inspections can reduce costs by identifying defects during the manufacturing process, before reaching end customers. This enables quick re-work at the factory site and reduces future return rates. It can also help to prevent costly product recalls with better quality products and save money in the long run.
Risk Management
Risk management is essential for your business to stand firm in the market. Quality inspections identify defect that could risk your business, enable correction actions to eliminate risks, and contribute to a healthy supply chain. This enhances brand reputation by meeting the customer’s expectations with high-quality products.
What are the most common types of quality control inspections?
A quality control inspector helps business owners by ensuring compliance and quality when they're not able to do so themselves. They do this by carrying out stringent inspections at various stages of the production process.
During a quality control inspection, quality control experts visit factories to check that the manufacturing process and products meet the agreed standard before the merchandise leaves the factory.
Their services include checking with detailed checklists to help you maintain and control product quality in your supply chain.
These inspections follow AQLs (Acceptable Quality Limits) which indicate an acceptable tolerance level for non-conformity or defects. Food and non-food production inspections follow the ANSI/ASQC Z1.4 (ISO 2859-1) statistical sampling procedure.
Depending on the buyer's requirements, factory inspections can take place at any stage of the manufacturing process. An organization may employ different inspections at each stage depending on factors like:
- The product characteristics
- Organizational interests
- Their history with the supplier or manufacturer
- Requirements specified by Amazon or another platform
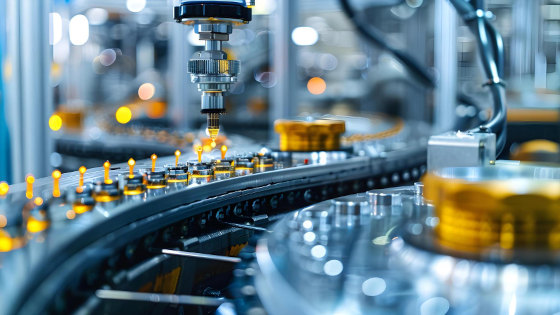
These are the most common types of inspections:
Pre-Production Inspection (PPI)
PPIs usually take place after you issue a purchase order and before the production runs. It is an integral part of your quality assurance management and risk assessment procedures.
A pre-production inspection assesses the quality and quantity of raw materials and components used during the manufacturing process. It compares the client's approved sample with the supplier's production sample to determine whether they conform to the product specifications.
These inspections are useful when working with a new supplier, especially if you have critical delivery dates. PPI inspections ensure the supplier is using the materials and components agreed to in your contract.
With a PPI, brands and retailers can reduce back-and-forth communications with their suppliers on quality expectations and raw material confirmation. This will give brands and retailers more visibility to their supply chain and enhance their supplier relationship.
PPI checklists usually include:
- Verifying the condition of raw materials
- Check the readiness of the factory's production line
- Check if the supplier has planned your purchase order
- Identify any nonconformity to avoid potential risk
Pre-production inspections play a vital role in ensuring clear communication between the development team, supplier, and manufacturer. If your materials don't meet the agreed-upon standard, you could end up spending money on expensive rework, experience increased returns and negative customer ratings.
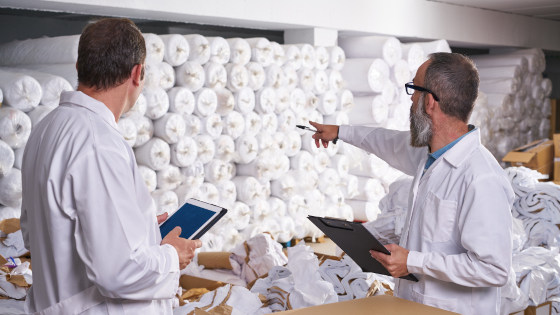
During Production Inspection (DUPRO)
DPI, or DUPRO, is carried out while production is underway. It's a useful step for products in continuous production, to identify any issues or risks early in the production process or if you've encountered quality issues during the PPI.
These inspections occur after 10-60% of the items are completed. This enables the inspector to identify deviations, provide feedback, and make sure defects are corrected.
During-production inspections ensure that manufacturers uphold product quality throughout the production process and help them identify any issues early on. In this way, you can avoid cost of non-quality, delays during production and also limit waste.
A DPI usually includes reliability and safety tests, verifying the production and quality plan, and inspecting the following:
- Storage conditions
- Semi-finished products
- Barcodes, labeling, and packaging
Pre-Shipment Inspection (PSI)
Pre-shipment inspections (PSI) are a vital final step before shipping the goods to the buyer. The process takes place when at least 80% of the order is packed and ready to go.
During these inspections, the inspector chooses random samples. They inspect each one for defects against the applicable ISO standards and procedures for manufacturing and packaging.
A PSI inspection includes verifying:
- Quantity of the products
- The workmanship of the products
- Shipping marks, labeling, and packaging
- Parts and components
- The functioning of the product
- Other specific manufacturing standards against the purchase contract
PSI inspections help you identify faulty products, so you don't pay for things you can't sell.
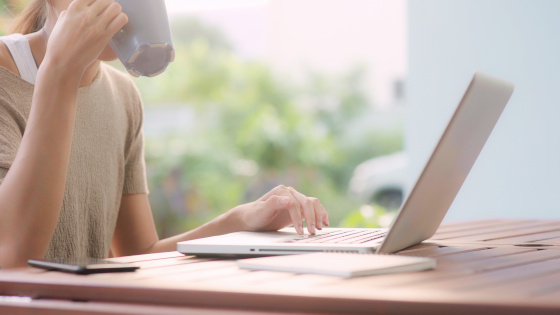
Fulfillment by Amazon (FBA) Inspections
Fulfillment by Amazon (FBA) is one of the best ways for Amazon sellers to maximize this platform. By outsourcing fulfillment to Amazon, sellers enjoy several benefits.
These include storing their goods in an Amazon FBA warehouse where Amazon employees will pick, pack, and ship them per order.
FBA sellers retain control over inventory management and pricing, but Amazon takes care of the rest.
Naturally, sellers pay extra for these conveniences, but they do enjoy easier access to Amazon Prime status for their products, streamline customer interactions, and enjoy a high level of trust from buyers.
All products that arrive at Amazon's fulfillment centers must meet Amazon's stringent FBA quality standards.
While Amazon does not stipulate pre-inspections, hiring an expert to carry out Fulfillment by Amazon inspections before your goods arrive at Amazon's warehouse is the best way to ensure you meet their criteria.
FBA has strict requirements when it comes to the way you label and package incoming goods. Hence, conducting an FBA inspection is a way to ensure your products meet these criteria when they arrive at the warehouse.
Repeated errors can lead to account suspension, so it's worth making sure you meet FBA standards beforehand. Plus, selling high-quality items helps you enjoy the benefits of good reviews on Amazon and repeat business from buyers.
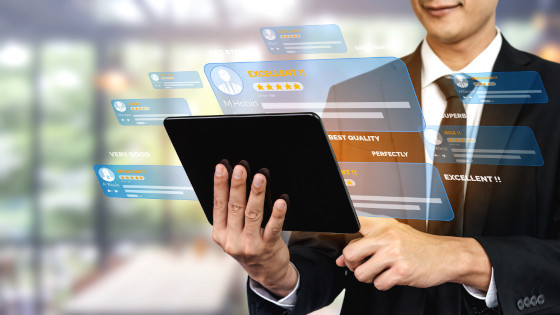
What Do FBA Inspection Services Include?
Most importantly, FBA inspection services help sellers meet FBA requirements and avoid having their products rejected, returned, or re-packaged on arrival. It will focus on checking the labelling and packing under FBA requirements.
Amazon has specific packaging requirements for different products and categories of products. For instance, every item in the Amazon warehouse has a unique FNSKU (Fulfillment Network Stock Keeping Unit), which identifies it as an FBA product. In an FBA inspection, the inspector will specifically check the FNSKU for the label size and information on it to see if it matches the products and FBA requirements.
If a seller markets similar items in different colors or sizes, each one must have a unique number. For tracking purposes, every package must display a scannable label or barcode that's easy to access. During an FBA inspection, the inspector will also check if the labels are scannable, and verify the information shown.
Additionally, Amazon has strict packaging rules depending on the category of the item. If it falls into several categories, it must meet the requirements for all of them. Whatever your product is, poly bagged units or set units, an FBA inspector will check if the product packing meets Amazon’s unique packing requirements.
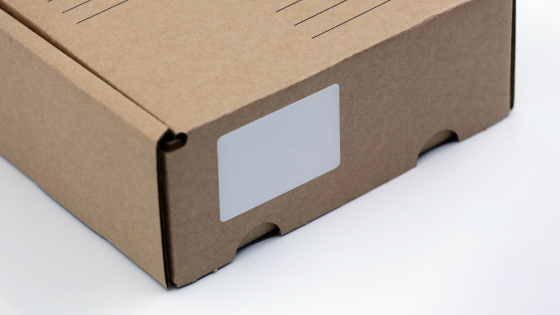
Due to these unique challenges, each FBA inspection and packaging service is customized according to the relevant product.
After an FBA inspection, sellers can access a detailed FBA inspection report confirming FBA compliance. The report should highlight any quality concerns and explain any labelling or measurement issues detected during the inspection.
These reports are invaluable for sellers who want to enjoy the benefits of FBA without fear of falling short of the requirements.
Simplifying the Quality Inspection Process
You can save time, money, effort, and stress by hiring a reputable inspection company like eAQF to help you enjoy the benefits of quality inspections.
We have 17+ years of experience in the consumer product industry, working with clients who source overseas, and across multiple product categories including Apparel, Home Appliances, Kitchenware, Toys, and Furniture.
It's easy to book your required service online. Simply go to our homepage, click on the type of inspection you need, and fill out the required information. We have easy-to-understand video tutorials on each of our booking pages to guide you through the process.
With eAQF, you can book and manage quality control solutions easily online, receive and review your quality reports instantly, and access real-time data 24/7. Are you ready to improve your e-commerce business with effective quality control? Register for eAQF today and get started!