What is AQL?
Acceptable Quality Limit, or AQL in short, is the most commonly used method to define random sample size for inspections and to define if the whole batches meet the client's quality requirements.
It is an industry standard based on ISO 2859-1 (ANSI/ASQC Z1.4-2003), published by the International Organization for Standardization (ISO).
The AQL indicates the maximum number of defects allowed in your products: a defect number below AQL will have a PASS report result, while a number over AQL will result in a FAIL result.
The AQL is not set in stone. Depending on different product types and different quality requirements, the AQL will differ and will affect the final result of the inspection report.
To start with, there are two inspection level types you can choose from: 'G - General inspection level', which is the most commonly-used, and 'S - Special inspection level' which is usually used for some particular types of product testing on a limited order size.
Then, you can see there are different inspection levels: GI, GII, GIII, and S1, S2, S3, S4. The figure represents the sample size. The bigger the figure is, the larger the sample size will be selected.
Based on the different values of your products, we suggest you apply the below AQL:
AQL Calculator
While the AQL chart can help you understand the numbers, an AQL calculator offers a faster and more accurate way to determine sample sizes. This easy-to-use tool lets you quickly calculate the required sample size by simply entering your lot size, inspection level, and AQL. The calculator then provides accurate sample size according to selected AQL standards, making it easier to streamline your AQL sampling process.
Quantity: | Inspection Level: |
Critical Defects | Major Defects | Minor Defects |
---|---|---|
Select AQL:
Sample Size: 0 units Maximum allowed: |
Select AQL:
Sample Size: 0 units Maximum allowed: |
Select AQL:
Sample Size: 0 units Maximum allowed: |
What are Minor Defects, Major Defects, and Critical Defects?
During an inspection eAQF inspectors will clearly define and classify the defects found during visual checks and on-site tests, and categories them as Minor, Major, and Critical.
Here eAQF will help to explain the most common ways to classify defects in different products:
-
Dent
-
Glue mark
-
Dirty spot
-
Poor paint
Minor defects
Minor defects are usually small and will not affect functionality and usability. They are mainly appearance defects, for example:
-
Broken stitches
-
Open seams
-
Deep scratch on item
-
Poor structure
Major defects
Unlike minor defects, major defects clearly deviate from product requirements and are likely to affect the performance of the products. Major defects can often result in bad ratings, customer complaints, product returns, and refund losses. For example, major defects can be:
-
Broken needles
-
Sharp corners or points
-
Damaged wiring
-
Power leakage
Critical defects
The quality control industry usually has 0 tolerance to Critical defects as they are non-compliance with mandatory regulations or laws. Critical defects can pose serious hazards to customers' health or safety, and cause product recalls & reputation crises. Common critical defects are:
As a professional quality control company, eAQF has developed standards for classifying various types of defects across different product lines. But as the brand or buyer, you are responsible for making the final decision to tolerate the defects found or not
How to read the AQL table and choose my sample size?
1. Refer to AQL Table A to select Sample Size Code
First, look at the first line to choose 'general inspection level' or 'special inspection level'. Most people will use 'general', as 'special' is usually reserved for particular types of product testing on a smaller portion of your order.
Each inspection level can be divided into different inspection types, no matter if it is general or special. From I to III and from 1 to 4, the bigger the figure is, the larger the sample size will be selected. 'General Inspection Level II', 'GII' in short, is the most popular choice. 'GI' is normally used when you have a limited budget and don't want to check a large sample size, and 'GIII' is used when you are more quality-focused.
Next, you may select your 'Lot Size' based on the quantity of your actual order.
For example, if you choose general inspection level GII and your order quantity is 2,000, your 'Lot Size' will fall into "1,201 to 3,200". Then you can find your sample size code letter 'K' when your lot size row and inspection level column meet.
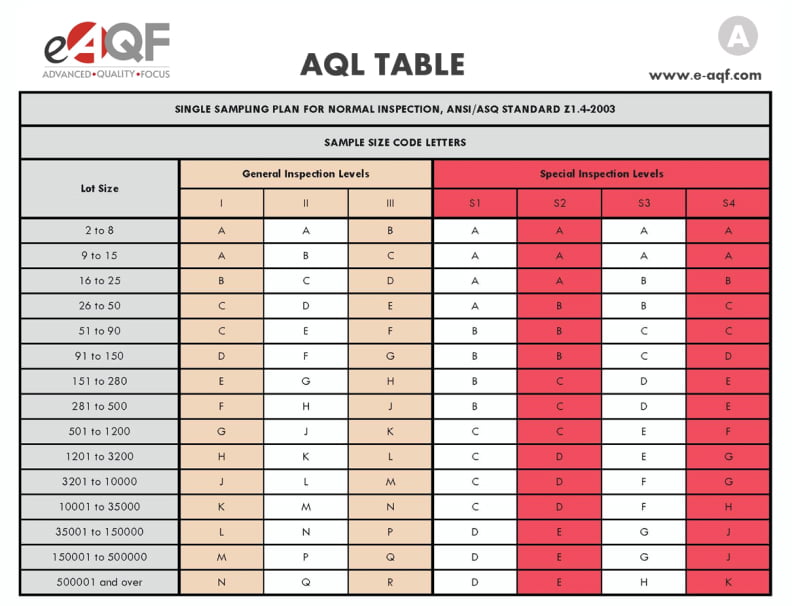
2. Refer to AQL Table B to select Sampling Plan
With your sample size code letter 'K', you will find '125' is your sample size, which means the inspector will randomly select 125 pieces from your whole order to conduct detailed checks and on-site testing.
Then, if you look at the first line of AQL Table B, you will find figures from 0.065 to 15, these are the AQL you are about to choose for your quality standard. These AQL figures mean the worst average percentage or ratio of defects that are acceptable for Minor, Major, or Critical defects. Each AQL column is split into 'Ac' (Accept) and 'Re' (Reject) so the inspector can define to accept and reject for a specific defect type by comparing the number underneath.
Let's say if you choose 1.5 percent for Minor defects, you will find corresponding numbers '5' and '6' when you cross reference row 'K' respectively. This means among the 125 samples, if 6 or more than 6 minor defects are found, your order may fail the inspection.
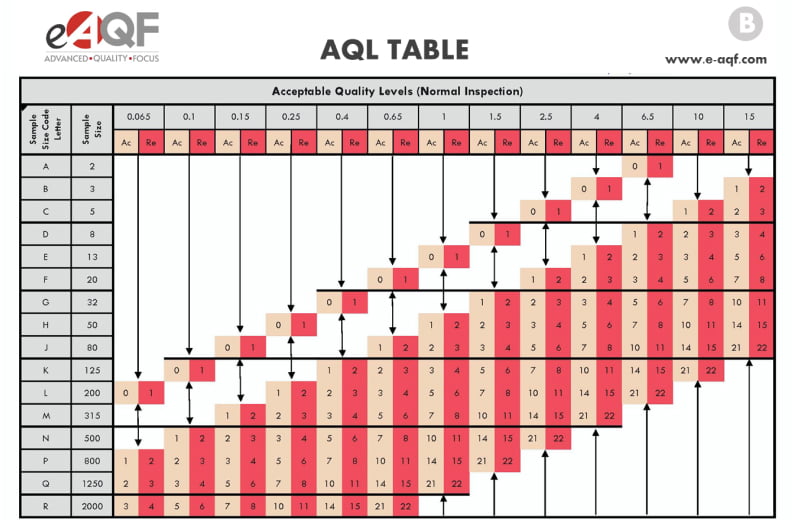